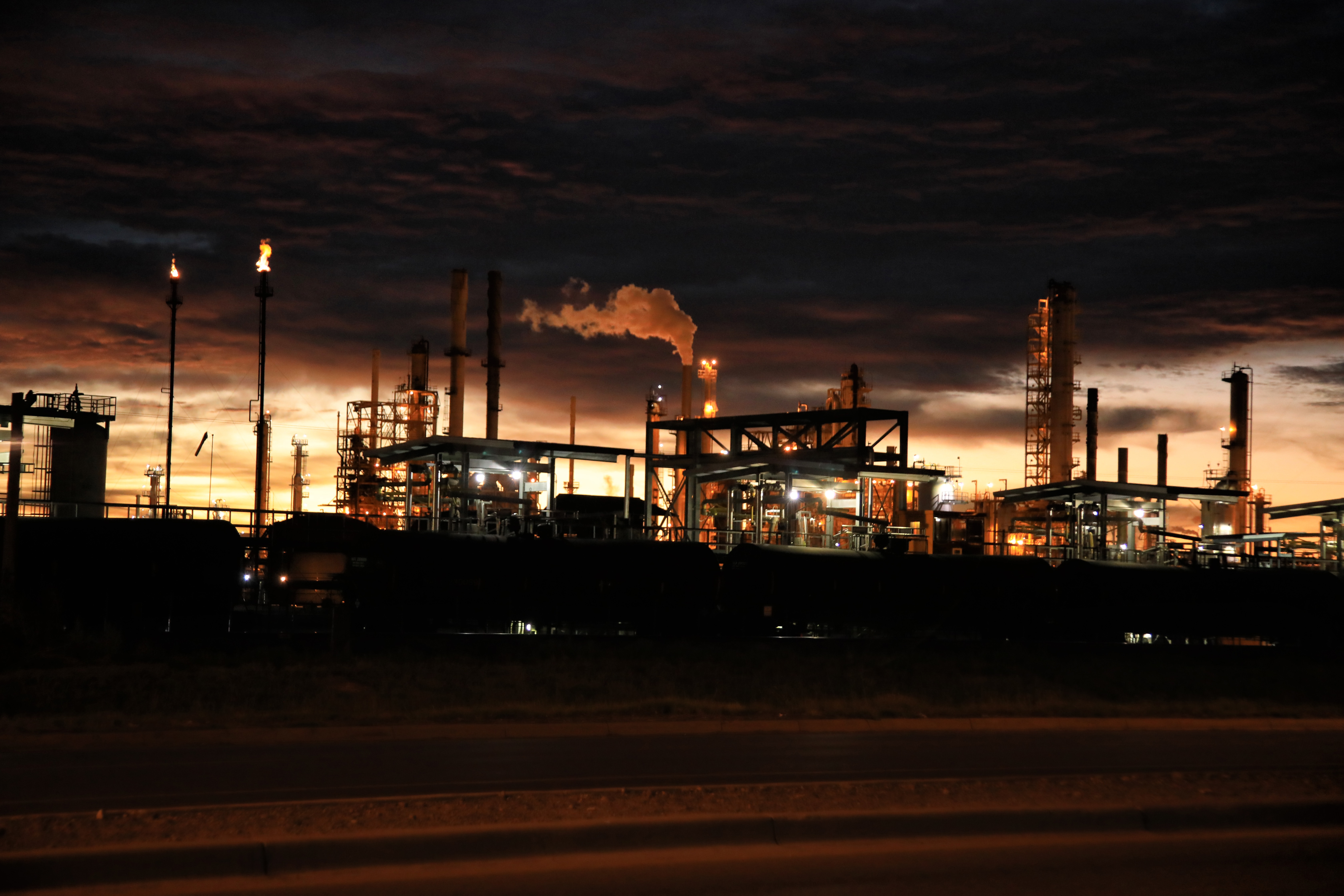
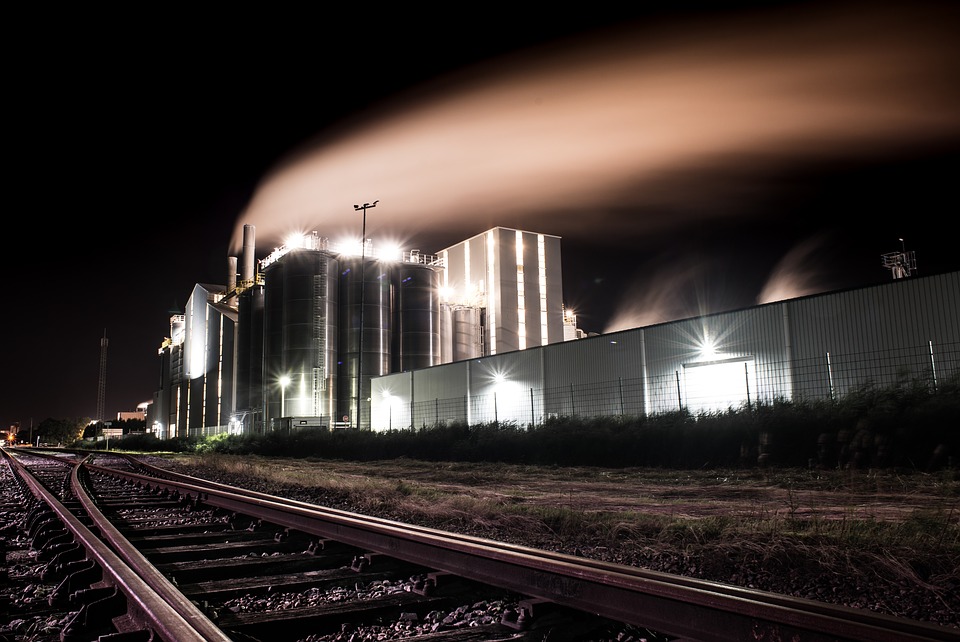
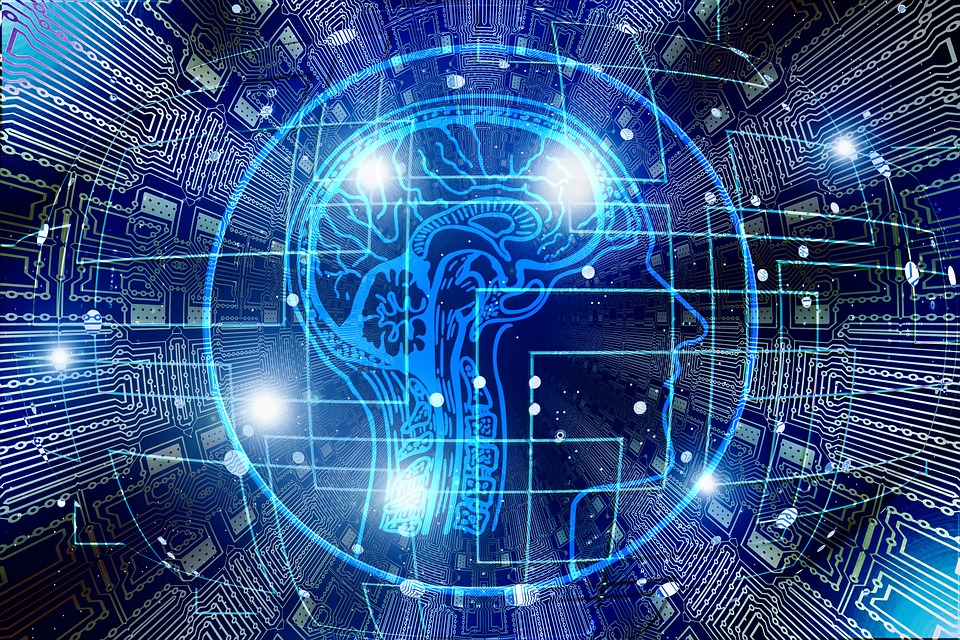
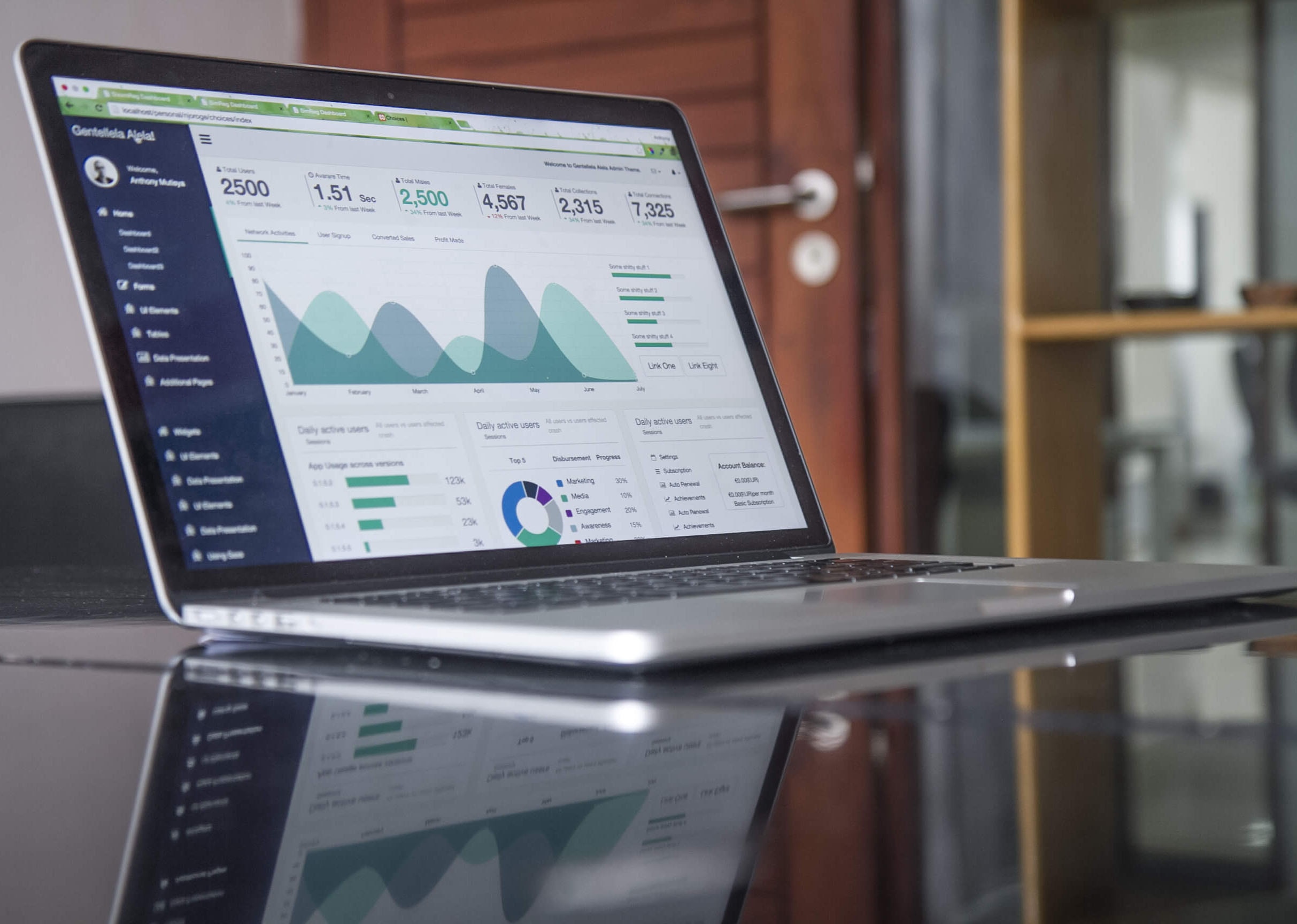
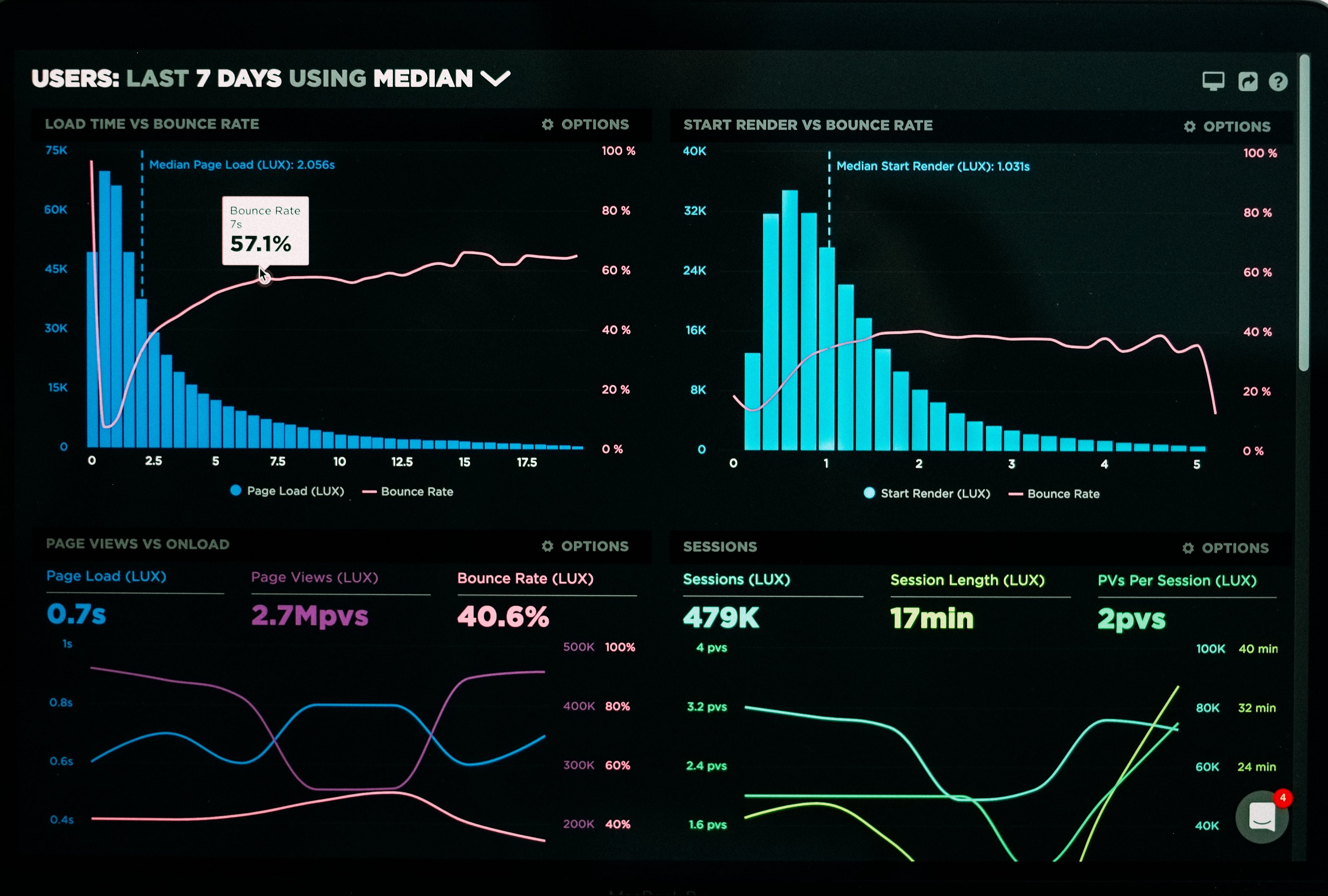
Using complex mathematical algorithms Convalis can determine whether your process is outside it normal conditions
Convalis develops mathematical models through large data sets in order to alert of abnormal conditions within your process
Convalis
In today’s environment many manufacturing sites have multiple IT systems carrying out multiple functions i.e. Maintenance, Maintenance Strategy, Condition Monitoring, Quality, OEE, Raw Materials Assessment and data manipulation. Because of having multiple systems, plants have teams driving the business using multiple systems in isolation to one another to help drive the business performance
The Convalis system is a flexible bespoke system that has been designed to work in three domains:
- Use data from existing or legacy systems owned by the site or their supplier’s systems to drive performance within Convalis
- Use a combination of existing system data and provide the additional modules within Convalis to drive the performance within the plant
- If there are no legacy systems data available or required then Meastim provide Convalis to deliver all required functions for the manufacturing teams to drive the performance and reduce the unit cost of the asset, with the objective of adding value to the business and reducing the amount of time spent on comparing data from multiple sources.
Raw Materials
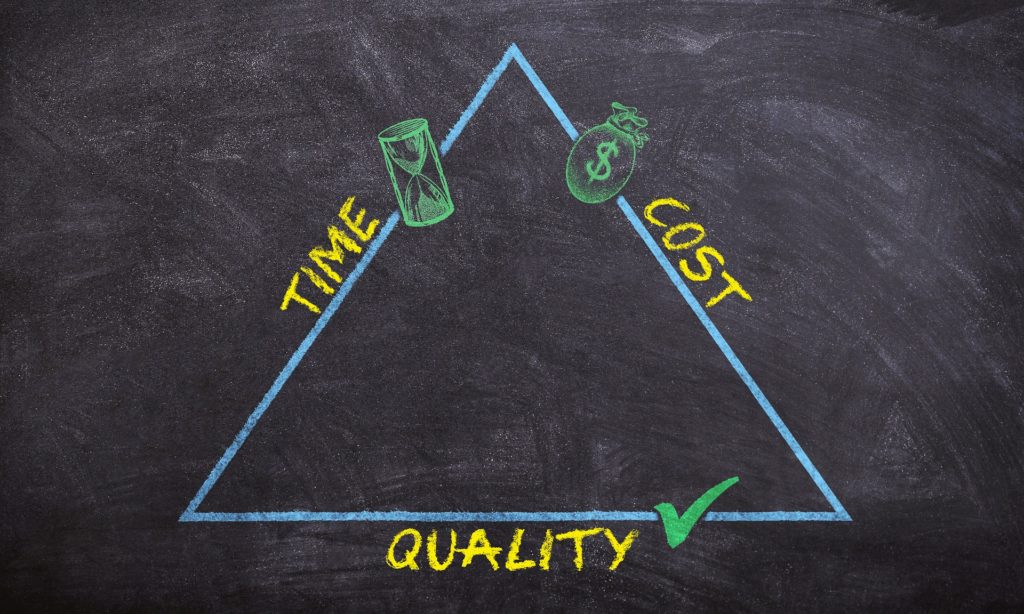
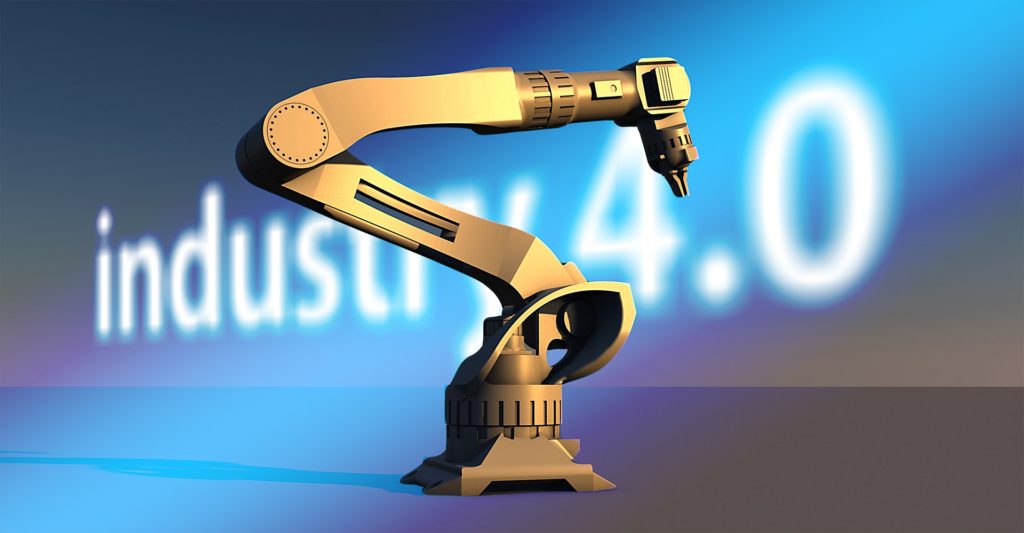
In today’s manufacturing world it is critical for a constant supply of high quality raw materials for production in order to minimise downtime and therefore maximising profits, it is important to have a supply chain that is able to keep up with demand while maintain quality inbound materials.
Convalis optimises the supply chain through live monitoring of the inbound raw material in advance of the material arriving at site to ensure the incoming materials meet all quality standards and prevent any wasted resources further down the production line.
Overall Equipment Effectiveness (OEE)
Overall equipment effectiveness is measured through the availability, performance and quality of a production it is essential to track all three factors in order to calculate an OEE score and make changes accordingly.
Convallis is now changing the existing model of gathering downtime data by operator input. We have moved to a model where downtime data is collected automatically such as stoppage, fault codes from your PLC and automatically corresponding it to any level on your asset register in order to automatically book production outages as well as link downtime into your maintenance management system.
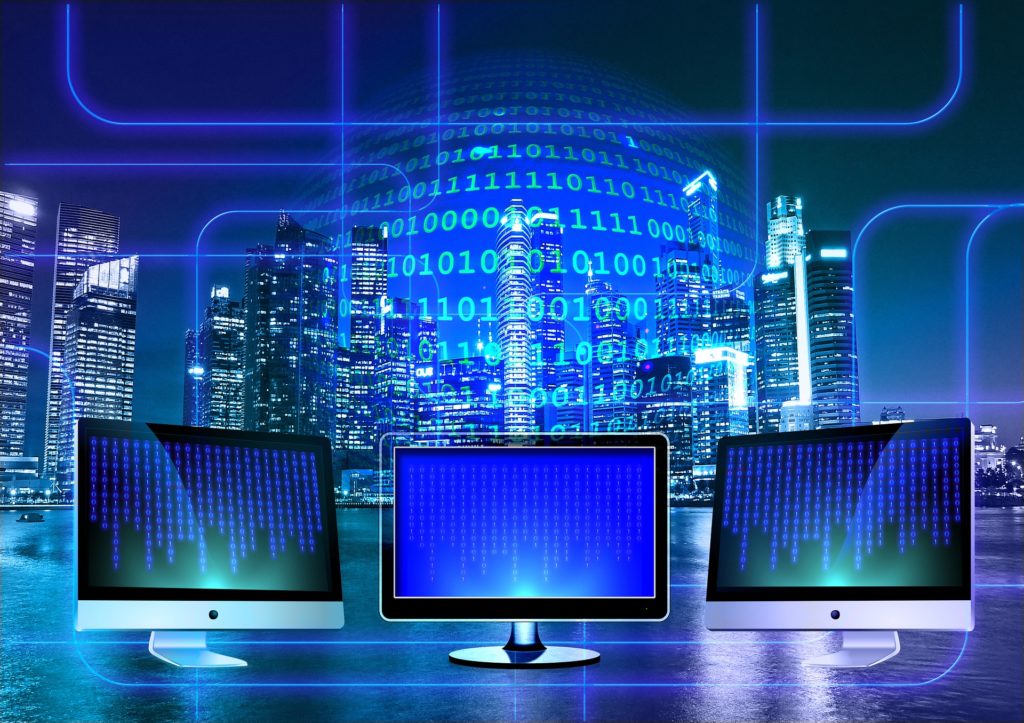
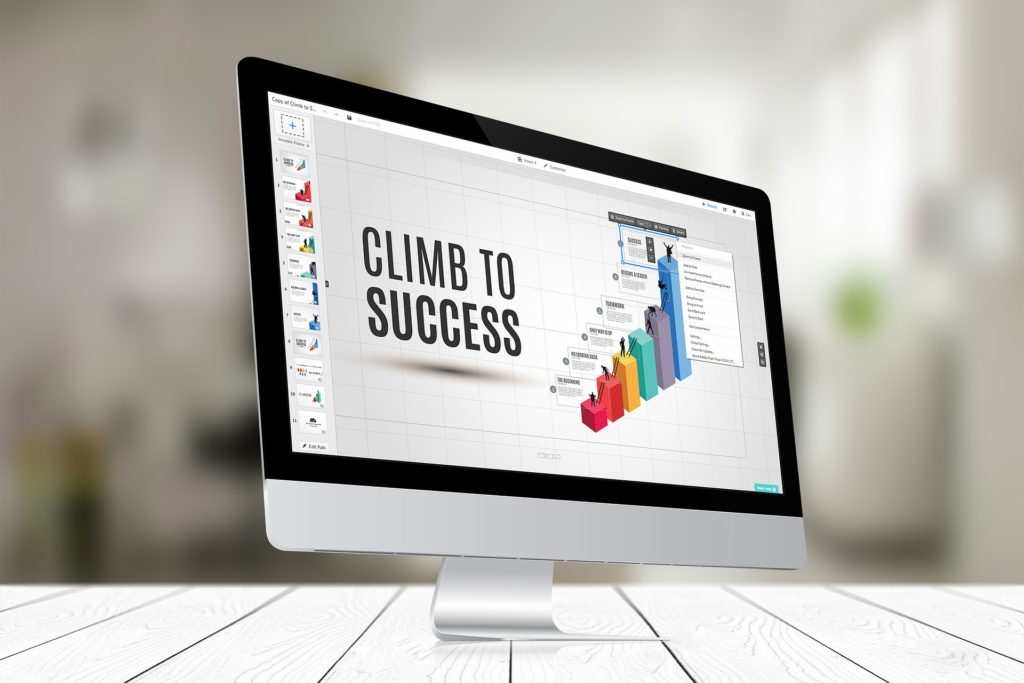
Data Analysis
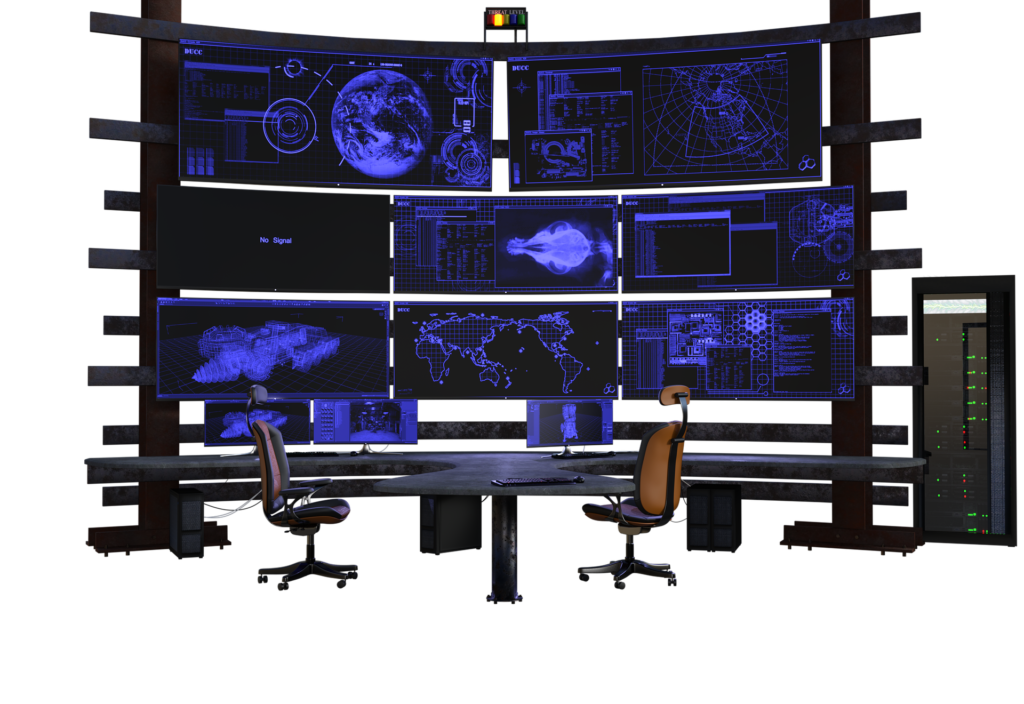
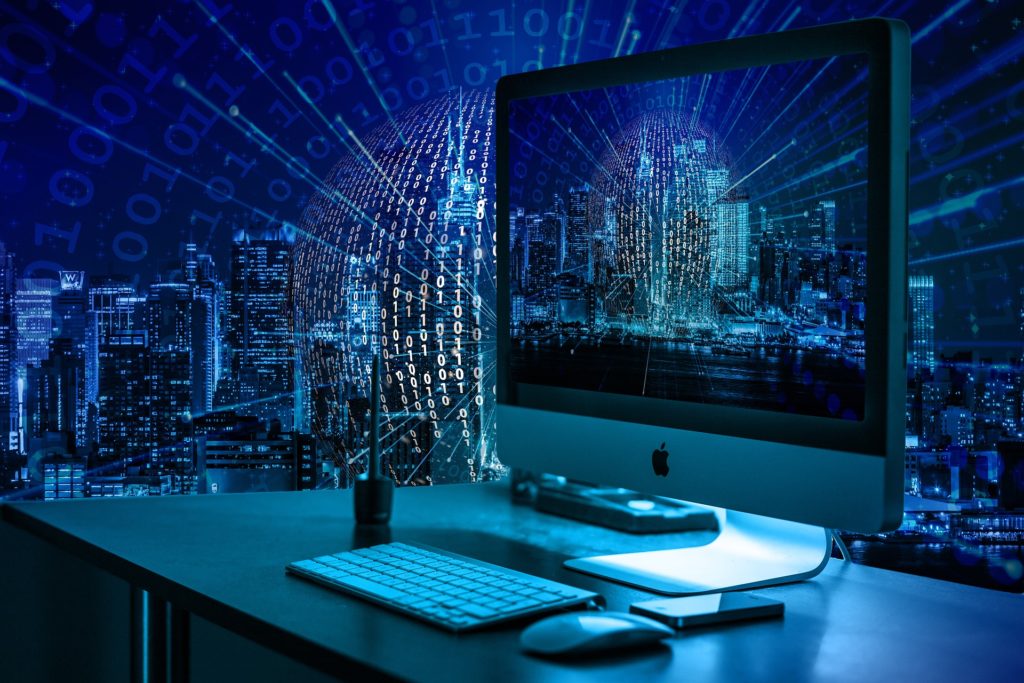
Being able to collect and dissect large data sets is essential in today’s manufacturing environment. It is important to understand the strengths and weaknesses in your production which will allow you to further optimise production.
Historian
A historian is critical in any situation where large datasets are used, it allows for data to be saved from multiple sources and synchronise them into one database with sync’d timestamps.
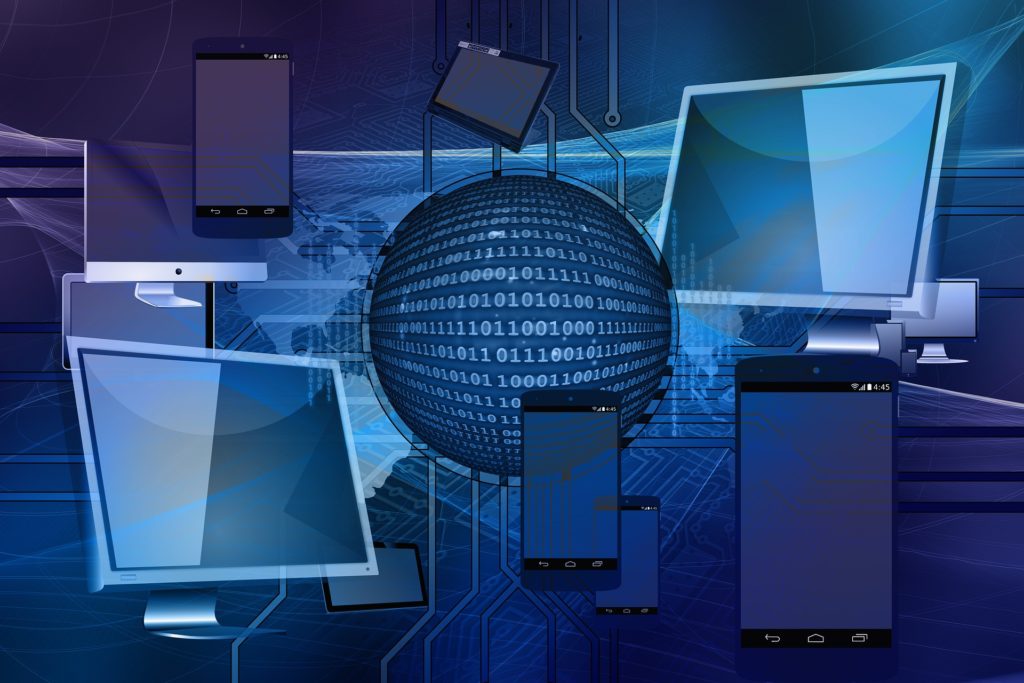
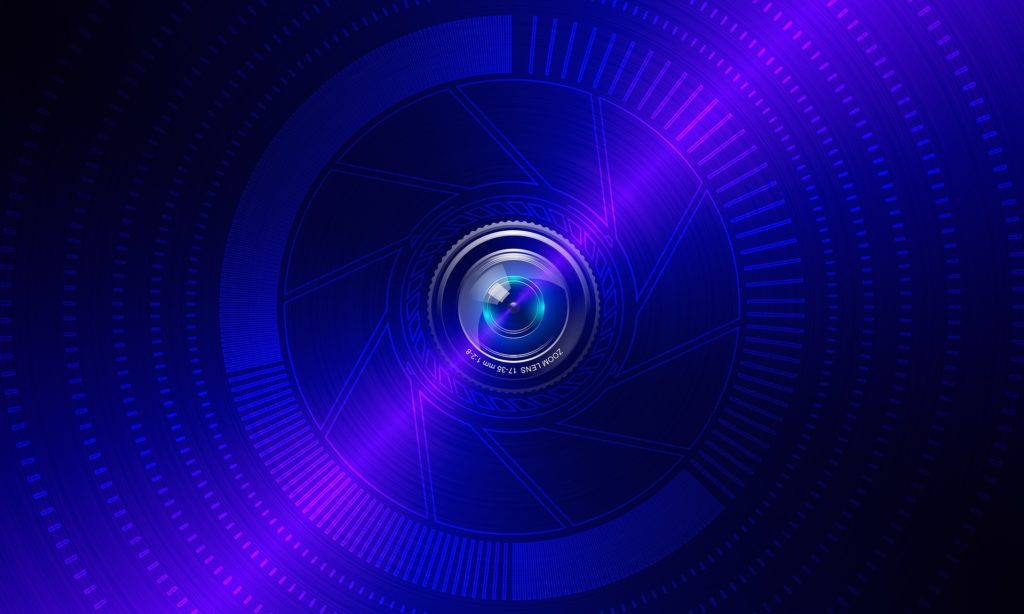